Two UNTHA XR waste shredders are now in operation for VPK Packaging Group in continental Europe, shredding pulped ropes as part of a closed loop paper production process.
Renowned for manufacturing 900,000 tonnes of paper per year from 100% recycled materials, VPK’s mill in Dendermonde, Belgium and Blue Paper Mill, co-owned with Klingele Papierwerke, in Strasbourg, France, naturally generate a waste by-product including complex pulper ropes.
This multifaceted 1:3 metal and plastic material was previously treated off site by a third party. However, the new shredding investment means that both sites can now process the waste themselves to manufacture an alternative fuel for their own energy generation.
At Dendermonde, untreated pulper rope waste is being fed into an UNTHA XR3000C shredder via a ceiling-mounted claw grab, at a throughput rate of five tonnes per hour. A 50mm screen ensures homogenous particle sizing before the fraction drops onto a horizontal discharge conveyor. The shredded material then passes up an elevated conveyor to an electro-magnetic FE-separator, where metals are extracted for onward sale and recycling. The finished product is an SRF specification fuel that VPK uses in its own on-site Waste to Energy facility.
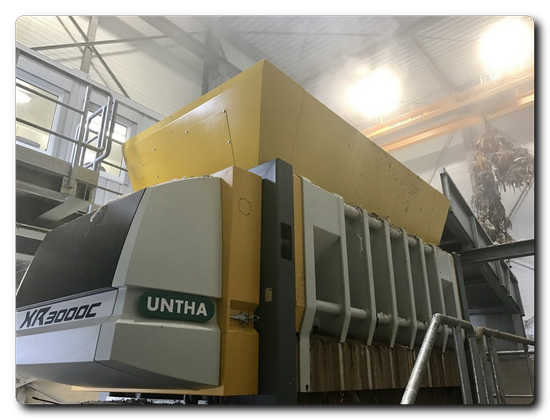
The SRF travels via a final horizontal conveyor into a bunker with walking floor to directly feed the plant. A level detector senses when the vessel is 70% full and the conveyor auto-reverses so that excess material can instead drop into a storage bay.
The complete solution including control cabinet room, steel support, service platforms, stairways and even the cranage sourcing, was supplied by UNTHA as a turnkey package. The tender stated a system capable of handling 5800 tonnes per annum (only during daytime working hours), but the VPK team is already confident that this target will be surpassed.
Commenting on the project, VPK’s Group Energy & Environment Manager Johan Dhaese said: “We are particularly impressed that we can process this waste material in a single step, as two shredders have traditionally been required for pulper ropes. We knew from a reference visit to another client site in Turkey, that this one-step methodology would be extremely effective, which is why we proceeded with the XR investment for both our Belgian and French sites.
“By bringing this process in-house we’ve benefited from cost savings, reduced the carbon impact of unnecessary waste transport and created an entirely self-sufficient closed loop too.”
UNTHA’s sales manager Daniel Wresnik, who was responsible for the project from the outset added: “Pulper rope shredding is a notoriously difficult, heavy duty operation which requires a robust and reliable machine. No two grabs of material are ever really the same, so the shredder must be capable of dealing with whatever is thrown at it.
“We’ve equipped the XR with two cutting rows and a torque+ gearbox for maximum torque on the shaft, which ensures performance without the need for high speeds. We have remote diagnostic capabilities should we need to advise on rotor speed or ram adjustments, for instance, but early indications suggest that the line’s only operator has this process fully under control.”
The complex nature of the input material was not the only challenge with this project. The footprint of the turnkey package was originally designed to sit outside in the open air. However, further research indicated the benefits of enclosing the line , which resulted in the construction of a 180sqm building to house the system. Adjustments therefore had to be made to the height, angle and lengths of the conveyors, and the shredder even had to be lowered into the building using a 100 tonnes crane before the building’s roof was installed.
UNTHA’s machine delivery in the Blue Paper Mill in France is virtually identical, apart from the fact that it will be handling approximately 4,500 tonnes of material per year.
Offering a concluding point, Johan said: “Recycling can become a costly and complex process for paper manufacturers, especially when handling waste such as pulper ropes. At the same time, we are always striving to minimise the net environmental impact of our operations – whilst reducing costs – so it made a lot of sense to manage the shredding, separation and SRF production ourselves. We’re delighted that we’ve been able to fully close the loop.”
VPK has purchased the two turnkey packages outright with an extended warranty package inclusive of service inspections provided by UNTHA’s Austrian engineers.